Continental develops pioneering technologies and services for sustainable and connected mobility of people and their goods. Founded in 1871, the technology company offers safe, efficient, intelligent, and affordable solutions for vehicles, machines, traffic and transportation. Continental generated sales of €37.7 billion in 2020 and currently employs around 235,000 people in 58 countries and markets. In 2021, the company celebrates its 150th anniversary.
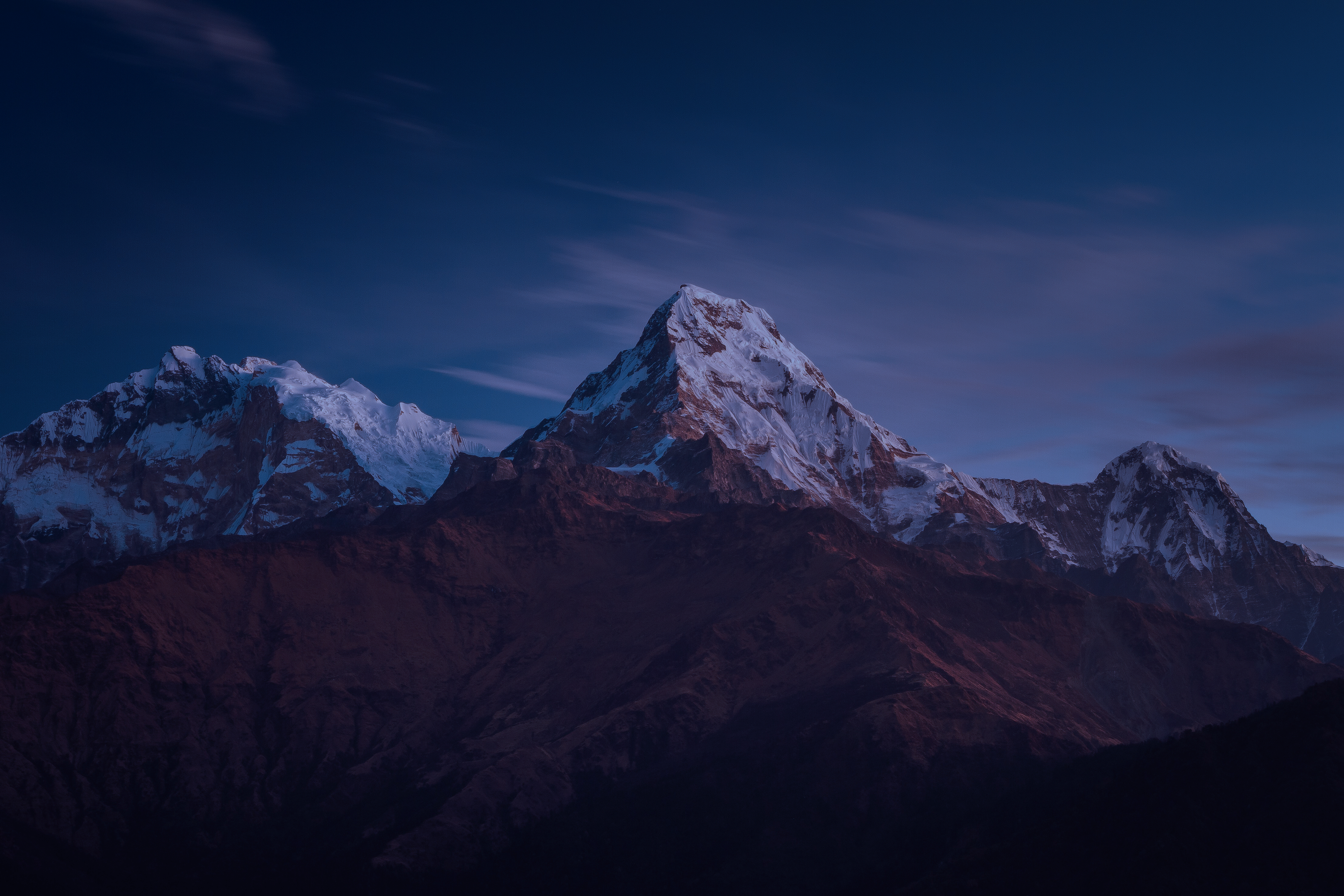
Representative
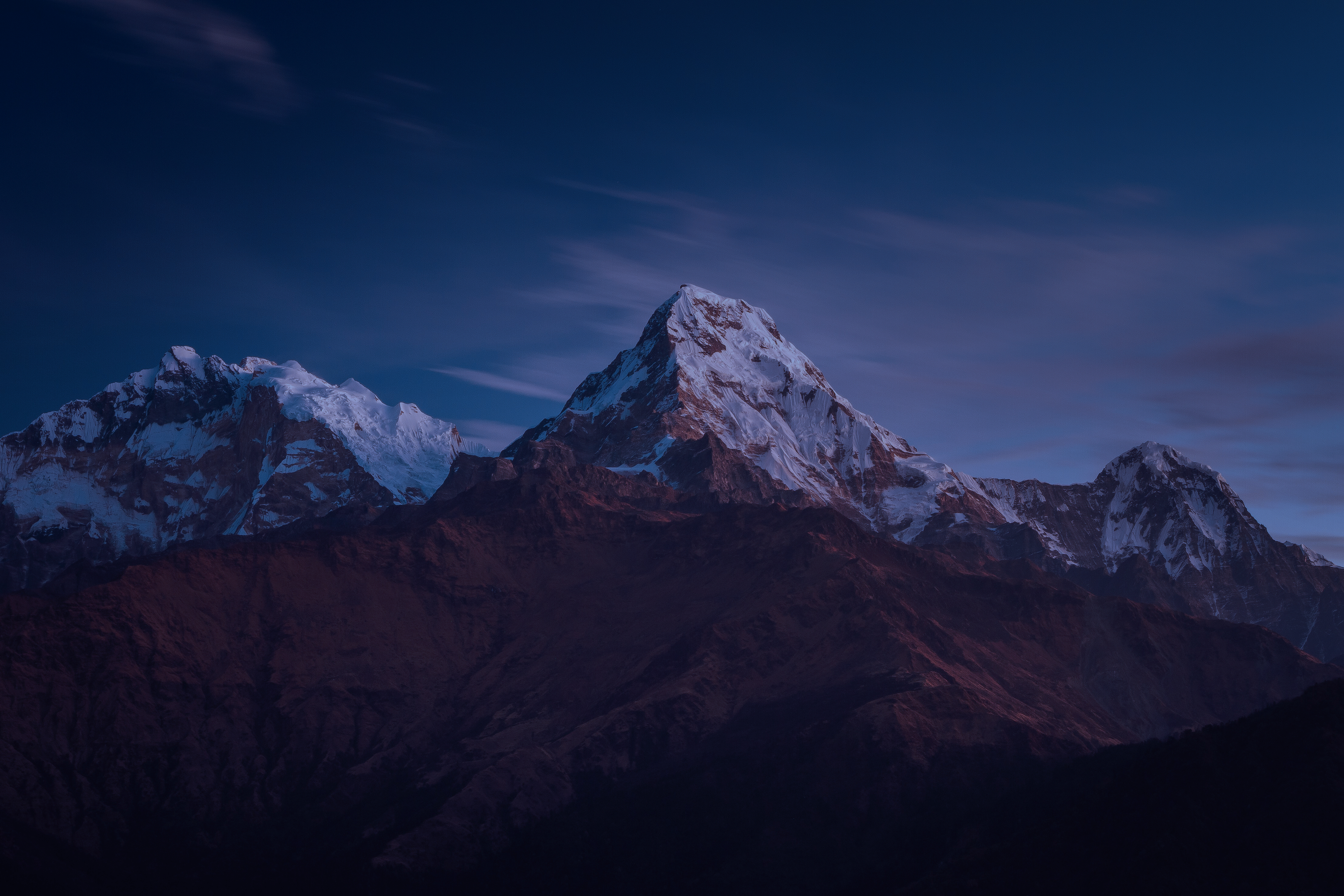
See FISITA Library items from Continental
F2020-VDC-076
Paper + Video
Dr.-Ing. Thomas Raste, Continental AG, GERMANY
Dr.-Ing. Andree Hohm, Continental AG, GERMANY
Dipl.-Ing. Alfred Eckert, Continental AG, GERMANY
Detail
FISITA World Congress 2021
VDC - Vehicle Dynamics and Controls
Downloads
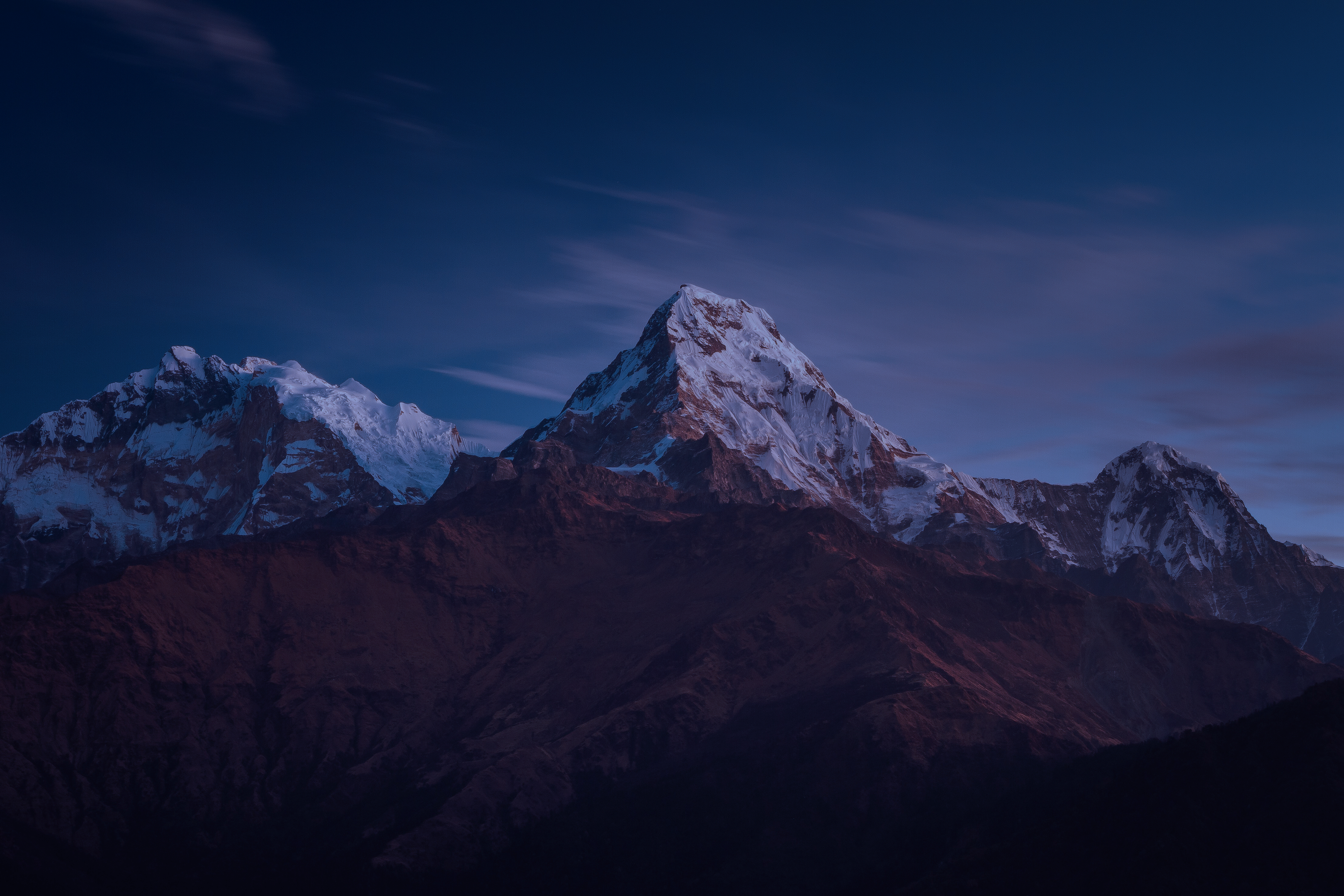
EB2022-IBC-008
Oral
S&P Global Mobility: Mr. Patricio Barbale
Detail
EuroBrake 2022
Braking systems as part of the mobility agenda (part 2)
Downloads
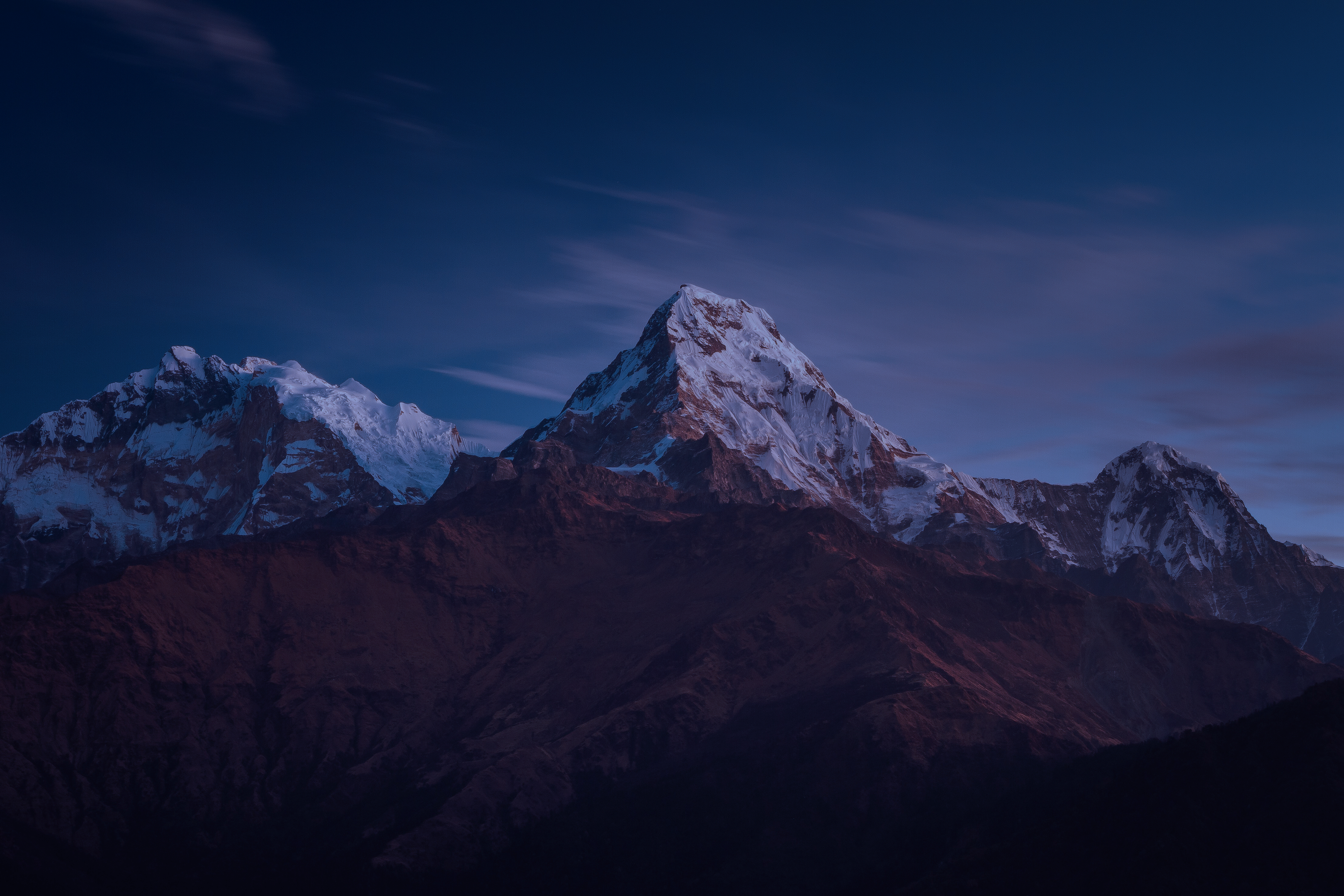
EB2021-IBC-006
Paper + Video + Slides
Detail
Mr. Lennart Guckes, TU Darmstadt Institute of Automotive Engineering (FZD), GERMANY
Prof. Dr. Hermann Winner, TU Darmstadt Institute of Automotive Engineering (FZD), GERMANY
Dr.-Ing. Jens Hoffmann, Continental Teves AG & Co. oHG, GERMANY
Mr. Sébastien Pla, Continental Teves AG & Co. oHG, GERMANY
During the development toward autonomous and electrified vehicles with low emissions, many visions for future mobility concepts arise, one of them being autonomous shuttles for urban areas. Most publications concerning these concepts focus on control and software while in this paper the change of requirements for wheel brakes is examined.
The performance of wheel brakes for todays passenger cars is currently tested under different worst-case assumptions regarding area of operation and highest possible load resulting from human operation. Considering the capabilities of autonomous shuttles like autonomous driving and the availability of regenerative braking, these assumptions need to be reevaluated. This also includes comfort and lifetime requirements regarding wheel brakes for these concepts and takes in perspective that for an autonomous shuttle a certain area of operation is defined in their operational design domain (ODD) as well as a lower maximum velocity.
To do so, different autonomous shuttle concepts are aggregated as well as their respective hardware and tech specs. To gather system requirements for the braking system of an autonomous shuttle a stakeholder analysis is performed, highlighting the underlying business model, driving tasks and passenger types as well as their needs and wishes. The shift in requirements is derived in comparison to conventional wheel brakes for cars. Usual performance tests for conventional wheel brakes for passenger cars are semantically analyzed to discuss their relevance and transferred into new performance tests for the given vehicle class.
Three test scenarios are created, the first one being the “Emergency Braking Test”, which consists of two consecutive emergency brakings. Secondly a “Standard Operation Test” which consists of ten consecutive, comfortable accelerations and decelerations for passenger pickup and transport. Lastly, a “Hill Descent Test” on a long descent in the area of operation of the shuttle, like in the demanding urban topology of San Francisco. Based on the scenarios different availability levels of regenerative braking power are considered.
Based on the developed test cycles a comparison is drawn for power and energy dissipation demand and the corresponding torques needed for an example vehicle under various levels of available regenerative braking power. While power and energy dissipation have decreased heavily, the torque demand is still as high as needed for a conventional vehicle.
The changed requirements open up new possibilities for suitable braking concepts for autonomous shuttles. This may also reduce brake emissions depending on the chosen concepts.
EuroBrake 2021
BCN
Downloads
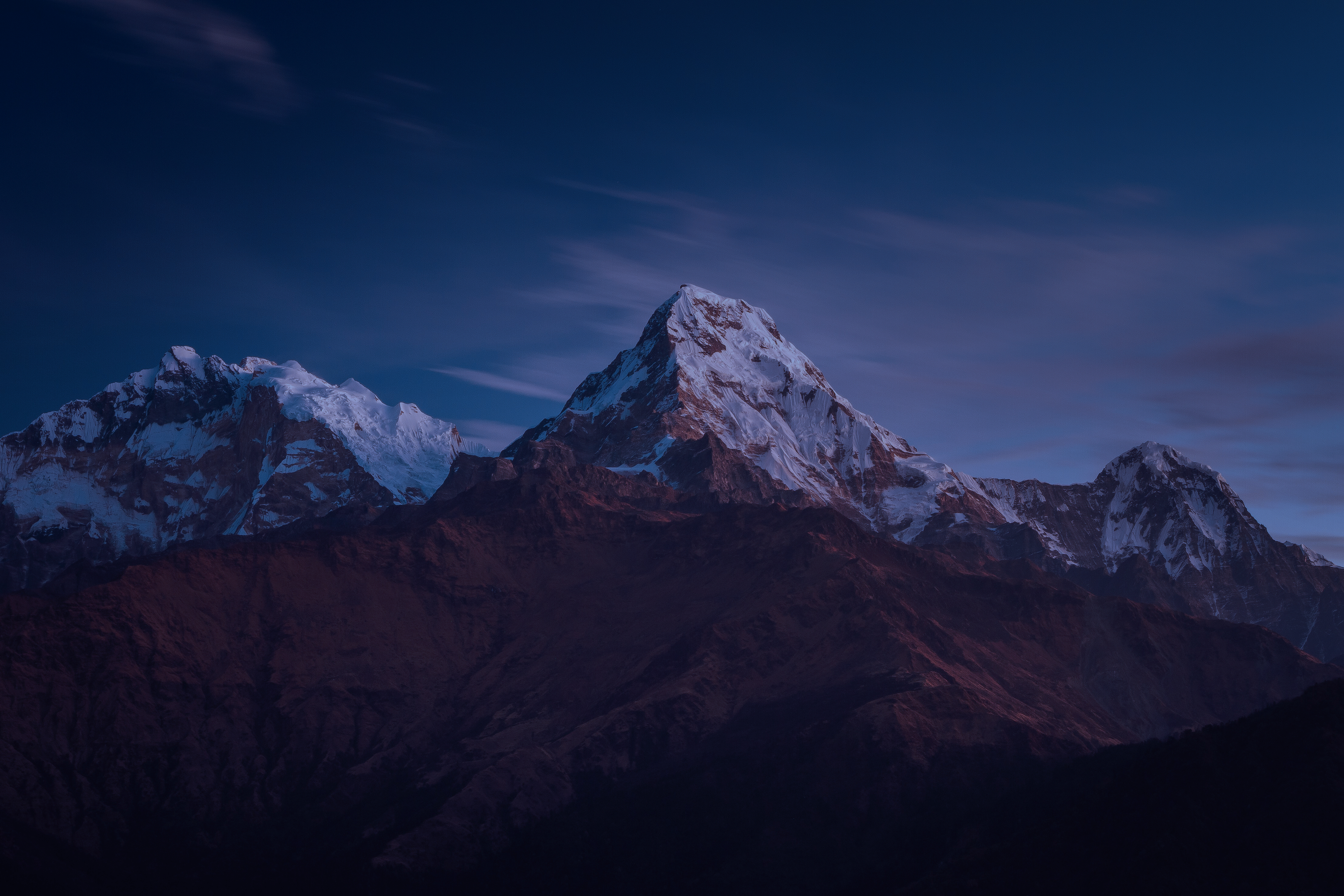
Error message goes here.
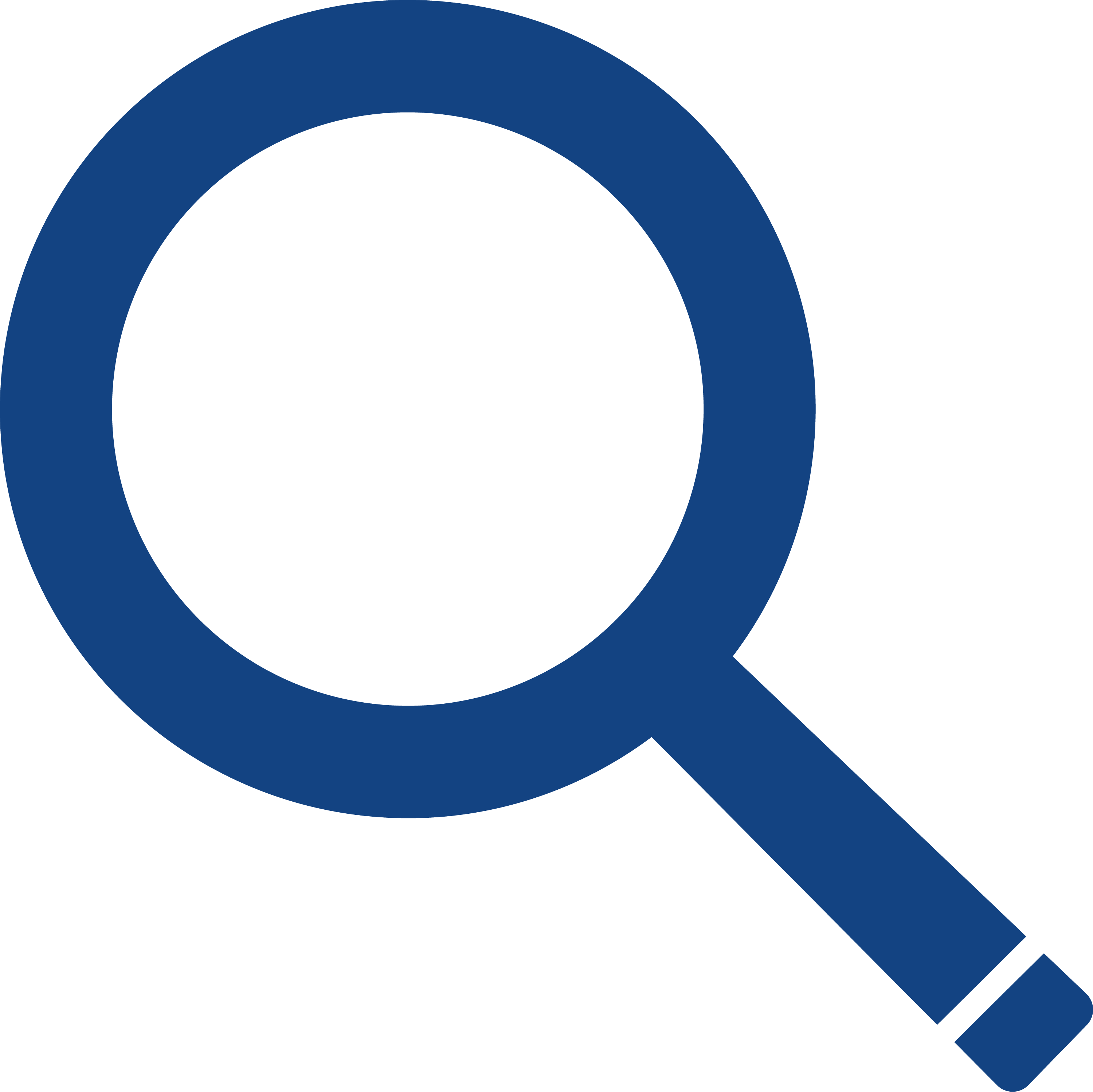
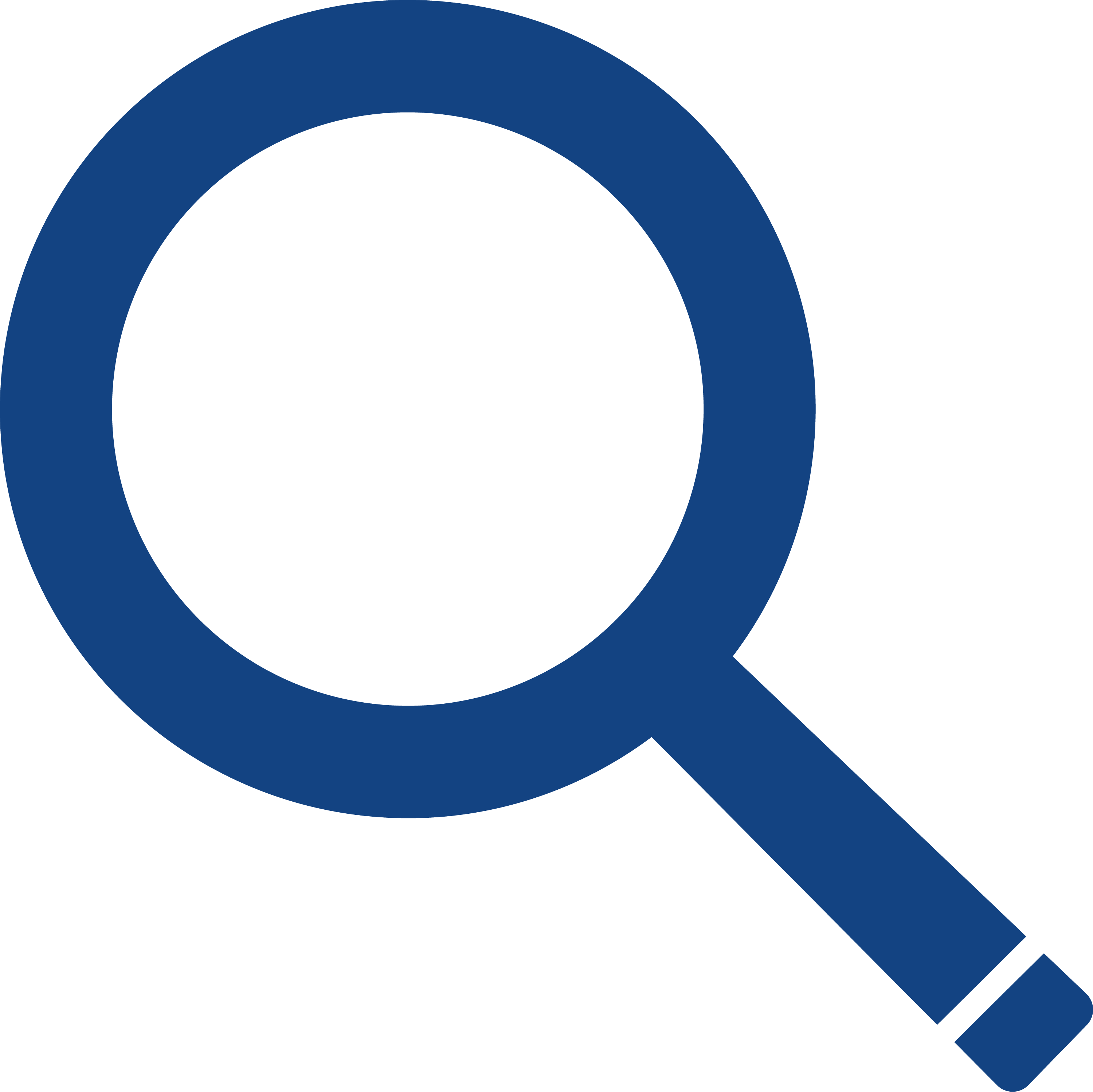
Message goes here.